With 5.8 million tonnes, whiteleg shrimp was the top species produced in 2020 (FAO). One of the most important operational functions in shrimp culture is the provision of adequate feed supply for optimal growth and it is also one of the main operational costs.
Shrimp aquaculture and hatcheries are still relatively new concepts within the animal nutrition industry, especially when compared to livestock. “We are learning the nuances of different environmental conditions across countries in various regions, as well as adjusting our strategies to meet the specific needs of each species, including their nutritional needs at every life stage,” said Thomas Raynaud, head of product management - Aquaculture, ADM Animal Nutrition.
There is a wide variety of hatchery feed procedures involving live and manufactured feeds and other additives. “For example, there can be a variety depending on the size of the tank, available feed, and facilities. There are also different methods of raising shrimp at the commercial level. For example, in Ecuador, farmers usually keep PLs in the nursery pond for longer, which means that when they transfer the animals, they are usually bigger and have an advantage over other PLs. In Mexico, there are lower temperatures and farmers use water heaters to control water temperature. What is most important is finding the right solutions for farmers based on their specific needs,” said Angel Gomez, managing director at Cargill Aqua Nutrition Latam North.
Between APAC and LATAM, each region applies a different mode of production at the hatchery level. “For example, in countries like Ecuador and India, there are vastly different environmental variables that affect shrimp production. Shrimp must be adapted to their respective environments in both areas and thus have needs that may vary from the other. We most often see this in the form of disease resistance, access to specific feeds and water quality stemming from different water sources, such as the Pacific and Indian Oceans that don't have the same mineral concentration,” Raynaud said.
Standardization
With all these different conditions and needs, would it be possible to standardize hatchery feed protocols? Industry stakeholders find it difficult for a number of reasons. “Every hatchery is its own unique biosphere, even each tank is its own biosphere and this is constantly changing according to conditions. I don’t see a cake recipe approach. It could be possible in broad terms but this is farming and will require a certain skill set and attention to detail that a fixed protocol can’t mitigate,” said Eamonn O’Brien, global product manager LifeStart at Skretting.
What can be standardized is the production of algae and Artemia. “Live feeds that are not properly produced are the major source of contamination of larval and post-larval shrimp. Protocols that ensure biosecurity for the production of algae and Artemia are essential, but other elements of hatchery protocols can not be standardized,” said Stephen Newman, CEO of AquaInTech Inc.
“In Asia, the most advanced hatcheries have dedicated live feed culture systems, some of the facilities are equal in size to the shrimp hatchery itself. Artemia, algae and polychaetes are grown (even bred) to produce a live SPF feed,” said David Danson, director of operations and shrimp at Hendrix Genetics. “In Ecuador, due to the great variety of specific conditions and products, it is difficult to establish standard operating procedures (SOPs) that would work well in every situation.”
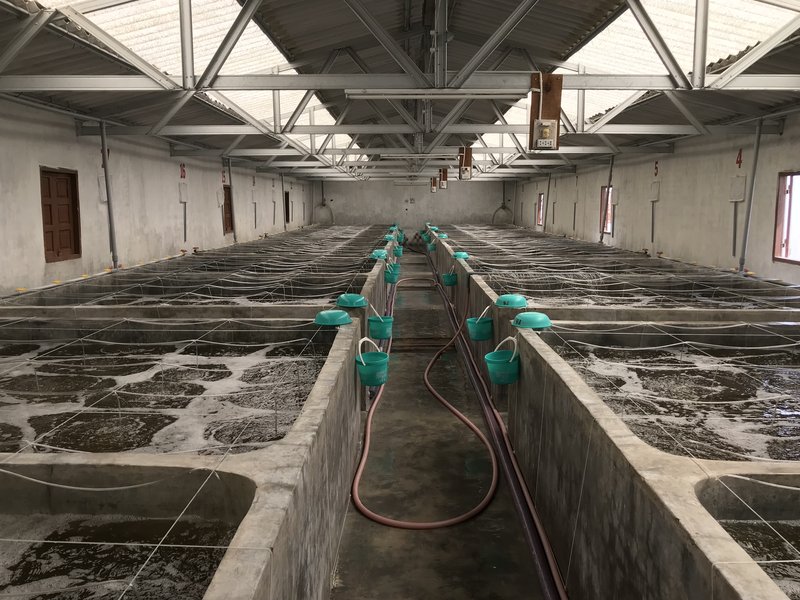
Credits: AquaInTech
Shrimp feeds and recent developments
New feed manufacturing technology has allowed the development of a new generation of feeds that can provide better nutrition and faster growth rates for shrimp. “Previously, farmers would use live organisms for feed, which could lead to transmitting diseases,” Gomez said. “In addition, there weren’t a lot of control tests to check if shrimp were contaminated or had an infection. A big focus in recent years has been on creating an artificial diet to reduce the risk of contamination.”
Shrimp feed processing technology has also evolved. “The aquaculture industry is quickly making a shift from pelletizer technology in favor of extrusion technology when developing new feeds for shrimp, with, for example in Ecuador, around 30% of the market using extrusion technology today. The industry was long challenged with pellet feeds, which struggle with water solubility as ingredients can leach out and lose their nutritional value. By making the switch to extrusion technology, we can maintain the integrity and stability of the feed when submerged in water but mostly when we are using an automatic feeder system. Extrusion also enables feed manufacturers to control the particle size of the feed, which is critical when formulating hatchery and nursery feeds,” Raynaud said.
“For nursery feed, cold extrusion is also becoming more prevalent. This approach uses lower temperatures to create feed options that are both digestible and nutrient dense with better behavior and stability in water,” Raynaud explained.
Technology has also allowed the production of small feed particles and liquid feeds. “The size of the feed is very important, and we now have the capacity to produce very small particles. This is an advancement from hard pellets that are broken up in the water, which leads to a lot of fine particles that are variable in size and leaching into the water. These technological advances allow us to get the right nutrients needed for the shrimp as quickly as possible, the same as with liquid feeds,” said Gomez. “Our liquid feeds are provided in gel form to avoid nutrients leaching out into the water, which helps promote faster growth rates as shrimp are obtaining all the nutrients they require.”
“Liquid feed delivers additives and different strains of probiotics in microcapsules that go directly to the larval gut and into the liquid matrix to improve the environment upon which the larvae depend. When applied properly, these advanced feeds can be a game changer for the hatchery,” said Ramir Lee, regional technical manager at Zeigler Bros., Inc.
“An area we have to look at is how we can help our customers operate more sustainably and lower their carbon footprint. One way we’re doing that is by developing feed that reduces the dependence on marine ingredients by using alternative ingredients. It reduces the carbon footprint and helps our customers and the shrimp industry operate more sustainably,” Gomez said.
“We, as feed suppliers, have a responsibility to prioritize the quality of our ingredients. It is crucial to maintain full traceability and ensure that we follow the necessary biosecurity measures. We also need to be realistic in terms of the claims made. We have to work with hatchery producers to get the best out of our feeds within a certain hatchery environment and continue to collaborate with them to ensure that everything stays on track,” O’Brien said.
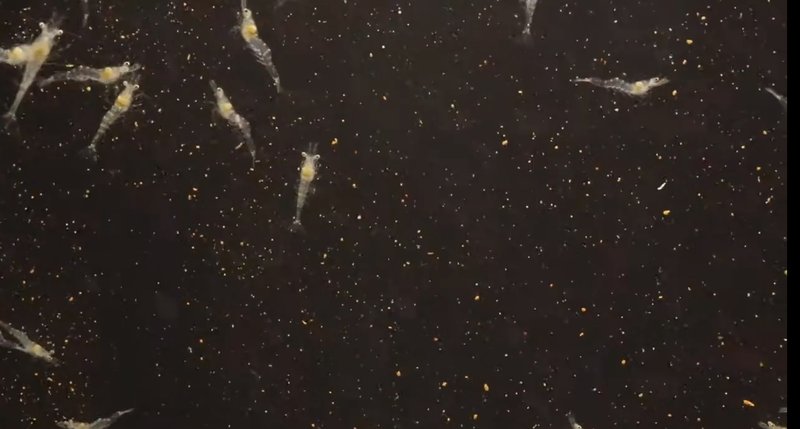
Credits: Zeigler Bros.
Eyestalk ablation
This technique has been widely used in the shrimp industry and some hatcheries are moving away from the practice, but there is still a long path until it disappears.
Why are shrimp hatcheries still using it? Robins McIntosh, executive vice president, Charoen Pokphand Foods (CPF) Public Company, said that farmers lose fecundity without ablation. “As we developed more fecund strains, you can operate a commercial operation with no ablation with feeds becoming more important in accomplishing this.”
Despite this, the industry seems to move to stop using this practice. “Ablation is no longer indispensable for most Ecuadorian strains. Also in Asia, we see that farmers can do without ablation when the broodstock conditions are optimal and most well-structured breeding programs supply stock that can do without it. This seems to be one of those traits where selection and husbandry have been successful. Reproduction without ablation tends to be more natural and the females tend to produce healthier and better offspring for a longer period when not ablated,” said Danson.
“The norm for many companies is mass mating. Females are placed into tanks with mature males. There can be a large number of animals in a single tank. This is not necessary. Females can be fertilized manually, individually or removed post-spawning and placed into 55-gallon containers. They spawn and it is then possible to track individual fecundity and spawning outcomes. By monitoring individual animals, one can select for animals that have high spawning frequencies without the need for ablation,” Newman explained.
“The global L. vannamei industry has significantly moved away from this practice in the past 4-6 years. We need to see some of our industry leaders publish on the performance benefits of this practice and I think we will see the practice phased out of the industry for L. vannamei completely. As P. monodon programs advance beyond the early stages of domestication, the same will happen for this species, however, there are fewer programs for this species and those which are established are typically still in earlier years,” said Melony Sellars, CEO and managing director of Genics.
“Improved reproductive output has enabled some companies to evolve strategies based on the use of non-ablated females. In some cases, this has resulted in improved broodstock health, reduced need for broodstock replacement, and corresponding improvements in nauplii production and vigor. The high cost of quality broodstock necessitates maximizing nauplii production. With or without eyestalk ablation, productivity per female over time depends upon healthy broodstock, optimal maturation conditions and high-quality broodstock diets,” Lee said.
New management tools
In recent years, data-driven platforms, smart feeding solutions, farm management software, satellite remote sensing and digital traceability solutions have been developed for the digitalization of the aquaculture industry and to improve production.
“There is huge room for farmer management and using new tools to help improve production. Unfortunately, the adoption has been slowed due to general farm economics and the investment required. In addition, there are many tools available that offer one solution, but not the whole solution,” Robin Pearl, CEO of American Penaeid, said.
“The ROI falls on the shoulders of the suppliers. Until the benefits are clear and justifiable, only a limited number of operators will adopt advanced technologies. One of the most important management technologies that, in many cases, reduced cost is the application of precision feeding. Overfeeding is one of the most important causes of environmental degradation, ammonia, and bottom fouling in the larval tanks. With new generations of premium feeds enabling improved efficiencies, more attention must be given to adapting and modernizing feeding protocols,” Lee said.
“As shrimp farmers benefit considerable production gains from the application of these new technologies, they can afford to invest in their use. However, it comes down to the cost recovery model for the technologies in use, when and how the farmer pays. The potential of the technological advances we are seeing today to change and shape the future of our industry is truly incredible and underpins in part the longer-term sustainability of our global industry,” said Sellars.
“Within the shrimp industry, there are regular debates on which production model, equipment, feeds and management strategies will be widely adopted in the future. Such decisions must consider fixed and operational costs, disease risks, environmental impacts, consumer trends, animal welfare and more,” Raynaud said.
“As the hatchery business becomes more and more competitive, the pressure to reduce costs grows. It is crucial for the competitiveness of the business and of the industry downstream that hatcheries do not compromise on quality. At the end of the day, hatchery profitability is most sensitive to PL survival. Maintaining high survival rates requires investment and efficient delivery of high-quality feeds,” Lee said.
“Farmers are very experienced people who understand shrimp and their farms. They must have access to accurate, reliable and cost-efficient information to take the correct decision. Without it, they rely on their experience solely. With the increasing price of all input and uncertainties caused by disease and erratic weather, approaches that were successful until recently require urgent revision. New digital tools are available to support the farmer decision process. They can improve the feeding, water parameter measurement or water oxygenation efficiency, leading to partial automation of some farming actions and higher efficiency,” Olivier Decamp, group technical director at Grobest, concluded.
Don't miss the previous articles in this series:
A look at salmon farming: Genetics, disease resistance and RAS
Tilapia farming I: Genetics, diseases and scale challenges